Have you ever paused to wonder how a simple sand derivative transforms into the dazzling glassware adorning your table? Or perhaps, what processes are involved in turning a blob of molten glass into a piece of art that holds your favorite drink?
Indeed, the question, “There are several ways to process glassware,” opens a window into a fascinating world of art and science. It is through a myriad of techniques that glassware achieves its final, polished look – a process complex yet awe-inspiring.
Let’s journey through this remarkable transformation, keeping your curiosity kindled and anticipation high.
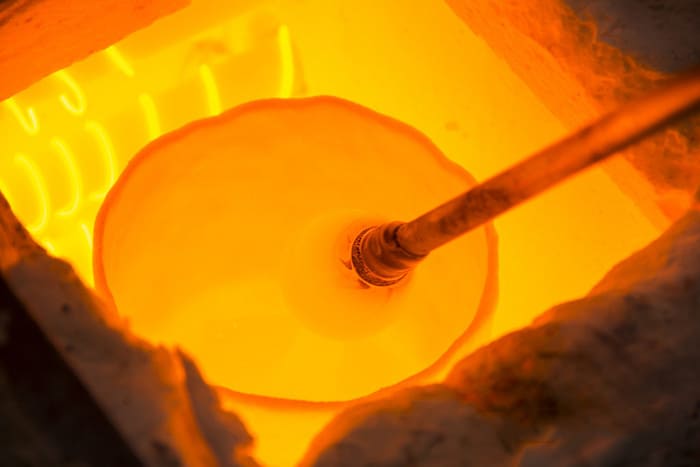
What Techniques Define Glassware Processing?
The process of glassware making is both an ancient craft and a modern industrial process. Techniques vary widely, but they all share the common goal: to create objects that are not only functional but also aesthetically pleasing.
Why Is Annealing Crucial in Glassware Production?
Annealing is a process that relieves internal stresses caused by uneven cooling. Without annealing, glassware would be prone to cracking or shattering with temperature changes or minor impacts. The annealing process involves slowly cooling the glass in a controlled environment, a step that is as crucial as it is invisible in the finished product. For more detailed insights on annealing, see resources here.
What Are the Steps After Initial Glass Shaping?
Following the formation of glassware, the removal of excess material, known as deburring or finishing, is essential. This can involve various methods from grinding to fire-polishing to achieve a smooth surface. For instance, the removal of the “moile,” or the leftover glass from where the piece was attached to the blowpipe, is done meticulously to ensure a flawless finish.
Can Glassware Be Strengthened?
Yes, glass can be toughened through thermal tempering or chemical strengthening. Thermal tempering involves heating the glass and then rapidly cooling it, inducing surface compression which makes the glass more resistant to breakage. Chemical strengthening is achieved by exchanging smaller ions in the glass with larger ones, typically through a salt bath, which also creates surface compression. These processes are pivotal in creating glass that can withstand everyday use.
How Is Artistry Added to Glassware?
To embellish glassware, engraving and cutting are employed. These techniques allow artisans to etch intricate patterns and designs, often turning each piece into a unique work of art. Whether through traditional diamond-wheel engraving or modern laser etching, the artistry involved is a testament to the skill of glassmakers.
What About Polishing and Satin Finishes?
Polishing can be achieved through several methods: mechanical polishing for a mirror-like finish, fire-polishing for a smooth and glossy appearance, and acid-polishing for a satin sheen. Each technique is chosen based on the desired outcome for the glass piece.
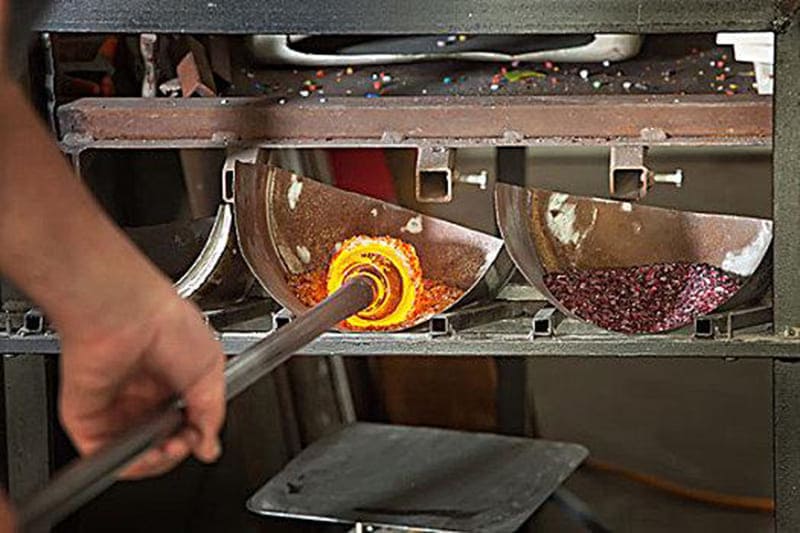
What Adds Color and Opaque Finishes to Glassware?
Frosting and satinizing methods, like sandblasting and acid-etching, create a translucent or opaque finish. These finishes can provide not only privacy but also a tactile quality to the glassware. Frosting techniques can be selective, with areas covered to remain clear while the rest of the piece is treated.
How Is Color Added to Glassware?
Color application to glassware can be achieved through spraying, rolling, or dipping in colored enamels or stains. The piece is then fired to set the color, resulting in a durable and vibrant finish. This can range from a simple one-tone coloration to complex, multi-colored patterns.
What Makes Glassware Iridescent?
Iridescence is introduced by depositing a thin layer of metallic compounds onto the glass surface, which refracts light to produce a rainbow of colors. This effect, often called “dichroic” glass, adds a shimmering, ever-changing quality to glassware.
How Are Precious Metals Used in Glass Decoration?
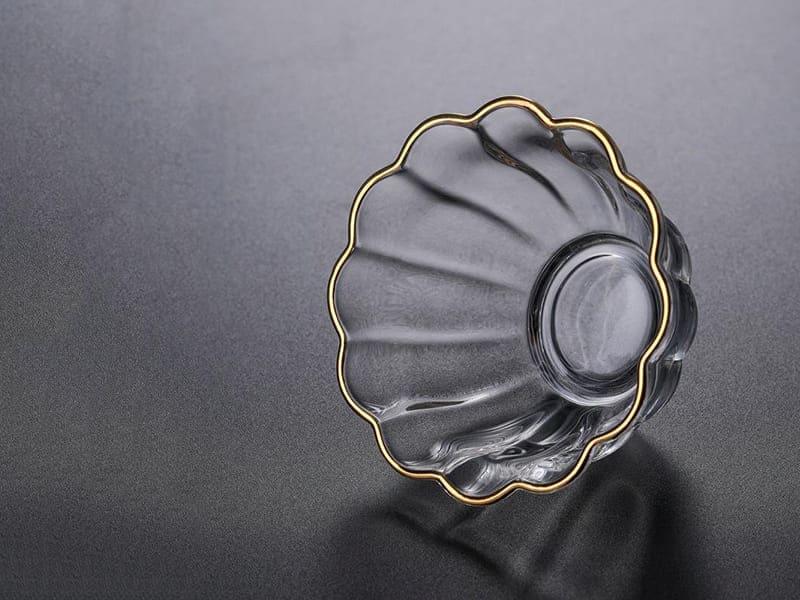
Gold and silver decorations are applied through techniques such as gilding and metallic staining, where metals are reduced to form a thin layer on the glass surface, yielding a luxurious appearance. The gold can be burnished to a bright shine or left matte for a subtler effect.
What Is Ion Diffusion in Glass Coloring?
Ion diffusion involves the application of metal compound pastes to the surface of the glass, which is then subjected to a controlled heat process. This heat causes the metal ions to diffuse into the glass surface, creating a colored layer. The depth and intensity of the color can be controlled by the temperature and duration of the heating process, as well as the type of metal compounds used.
The advantage of ion diffusion over other coloring methods is the durability of the color. Because the color penetrates the surface of the glass rather than sitting on top of it, it is less susceptible to fading and wear over time. This makes ion diffusion particularly valuable for items that will be exposed to sunlight or frequent handling, such as drinking glasses or decorative windows.
The Art of Glass Engraving
Following ion diffusion, another decorative technique is glass engraving. With the use of a diamond-tipped stylus or rotary tool, artists can etch intricate patterns, text, and images into the surface of the glass. This subtractive method removes parts of the glass surface to create a design that can range from simple monograms to complex scenes.
Thermal Shock for Crackle Glass
Thermal shock is deliberately induced to create crackle glass, a decorative style characterized by a network of fine cracks in the glass. This is done by submerging hot glass into cold water, causing the surface to crack. The glass is then reheated to seal these cracks within the outer layer of the glass, ensuring that it remains structurally sound while exhibiting a fascinating crackled appearance.
Chemical Etching for a Frosted Look
Chemical etching is another technique used to achieve a frosted look on glass surfaces. Glass is treated with hydrofluoric acid or a similar etching cream, which eats away at the glass surface to create a matte finish. Patterns and designs can be created by applying a resistant stencil to the glass before etching, allowing for precise and intricate designs.
Glass Painting for Exquisite Detail
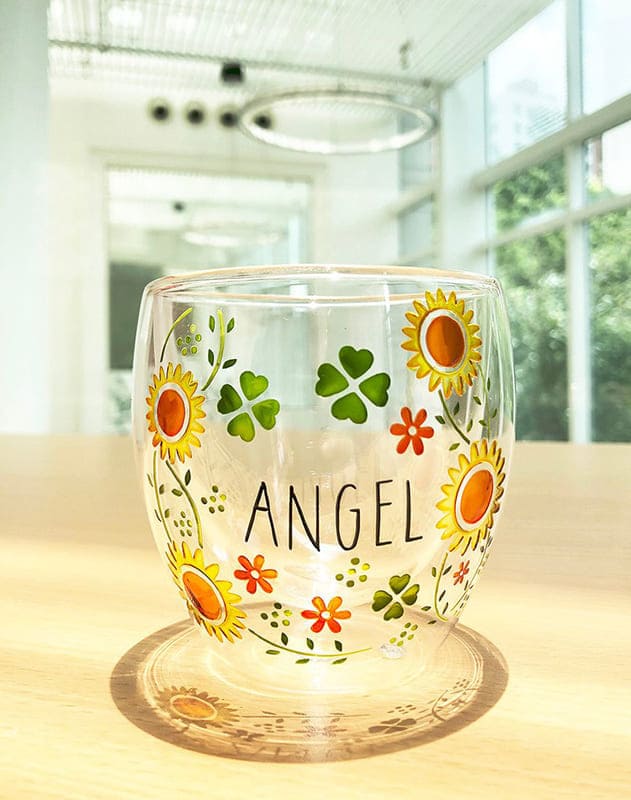
Glass painting involves applying special paints to the surface of the glass. These paints are then set by baking the glass at a low temperature. The paints used in this process are formulated to bond with the glass surface, allowing for the creation of colorful and complex designs that are more detailed than those typically achieved through colored glass techniques.
Through these varied techniques, glass can be transformed into works of art or functional pieces with enhanced aesthetic appeal. Each process contributes to the diverse world of glass craftsmanship, reflecting both traditional methods and modern innovations.”
These methods highlight just a fraction of the countless ways glass can be manipulated to fit the functional and aesthetic needs of cultures around the world, continuing a long tradition of glass artistry that stretches back centuries.